Fonderie de précision à la cire perdue et défauts de fonderie
I. Généralités définitions :
La fonderie à la cire perdue est une méthode qui permet de reproduire en métal, une maquette en cire, et, ce, à un unique exemplaire.
Introduite dans notre profession par Taggart en 1907, cette technique a été modifiée par certains auteurs qui tentèrent de compenser le retrait du métal entre le liquidus (courbe expérimentale obtenue par analyse thermique, en joignant tous les points de solidification commençante lors du refroidissement d’un alliage à différentes concentrations) et le solidus (celle de la solidification finissante). Puis entre le solidus et la température ambiante.
II. Principe
Le principe consiste à éliminer la cire de la maquette préalablement noyée dans un matériau réfractaire à l’état fluide et constituant après durcissement, un moule parfait, et communicant avec l’extérieur par un tunnel dit « tunnel de coulée », puis dans le volume vide ainsi crée, à faire pénétrer le métal en fusion par l’intermédiaire du tunnel de coulée.
Après solidification du métal et destruction du moule, on obtient une pièce métallique théoriquement identique à celle de la maquette originale.
III. Technique
A. Cas de maquettes de dimensions réduites
1. Elaboration de la maquette
Réalisée en bouche (méthode directe) ou au laboratoire sur un modèle (méthode indirecte), la maquette en cire sculptée, sera désolidarisée de la préparation dans l’axe de dépouille, au moyen d’une tige métallique légèrement enfoncée dans les parties épaisses de la cire. Secondairement une, nouvelle tige pourra remplacer la première. La longueur sera telle que le chemin à parcourir par le métal soit de 1.5 cm en moyenne. Pour éviter les défauts, la tige pourra être pourvue d’une masse sphéroïde en cire qui servira de nourrice.
La surface de l’ensemble sera dégraissée à l’aide d’un mouillant. La tige supportant la masselotte sera solidarisée au moyen de cire par son extrémité libre au sommet d’un socle conoïde en buis, caoutchouc vulcanisé, en résine ou en métal.
2. Mise en revêtement de la maquette
Sur le socle vient s’ajuster un cylindre ouvert aux deux extrémités servant de récipient au revêtement réfractaire qui enrobera la maquette préalablement enduite au pinceau de ce même revêtement.
Le cylindre est tapissé d’une épaisseur humidifiée d’une bande à cylindre (liner).
Introduit à l’état relativement liquide, de préférence sous vide et vibré, ce revêtement durcira secondairement emprisonnant la maquette et la tige de coulée munie de sa masselotte.
Si on emploie la méthode hygroscopique, c’est avant le début de la prise du plâtre que le cylindre sera soit immergé dans l’eau à 37° pendant 30 mn minimum, soit submergé à son extrémité opposée au cône.
La partie basse de la maquette sera environ à 6 mm de la surface du revêtement opposée au cratère. Et la nourrice au centre thermique du cylindre.
3. Elimination de la cire
Après durcissement complet du revêtement (1 h environ), la tige de coulée est désolidarisée du cône, nettoyage du cratère, la tige est retirée en la chauffant légèrement à son extrémité libre.
La cire est éliminée par le tunnel ainsi crée en chauffant progressivement (de 20° à 700°) le cylindre placé sur une grille cratère vers le bas. Les résidus peuvent être éliminés en plongeant le cylindre dans l’eau bouillante, en utilisant la centrifugation ou la vapeur d’eau.
4. Chauffe des moules réfractaires
La température de préchauffage dépend de l’intervalle de fusion de l’alliage :
- En ce qui concerne les alliages précieux à basse fusion destinés aux inlays, inlays-core, couronnes, petits bridges et métallocéramiques basse fusion, leur intervalle de fusion se situe entre 800 et 1000 °C. Leur température de préchauffage conseillée est de 650 à 700 °C.
- Les alliages précieux destinés à la technique céramométallique ou les alliages non précieux nickel-chrome, dont l’intervalle de fusion est situé entre 1050 et 1350 °C, doivent impérativement être coulés dans des revêtements à liant phosphate préchauffés entre 780 et 820 °C.
Il vaut mieux mettre en chauffe un cylindre 1 heure après sa mise en revêtement que d’attendre le lendemain pour le couler. La chauffe se fait avec une augmentation graduelle de la température respectant les paliers préconisés par le fabricant de revêtement pour que la chaleur extérieure puisse pénétrer d’une façon homogène le cylindre.
5. Coulée
La masse du métal à couler (environ 2 fois le volume de la maquette) est alors déposée dans le cratère même du revêtement ou dans un creuset communicant avec le cratère du cylindre et la fusion est réalisée au moyen d’un chalumeau ou d’un four à induction à haute fréquence annexé à la centrifugeuse.
Sauf dans le cas de la fusion par induction où cette précaution n’est pas nécessaire, on protègera le métal en fusion de l’oxydation au moyen d’un flux réducteur (borax en général).
Dès que le métal est en fusion complète, sans surchauffe, on fait démarrer la centrifugation ou l’admission de la pression selon le type d’appareil utilisé.
6. Démoulage de la pièce coulée
Après arrêt de la centrifugation, le cylindre est plongé dans l’eau froide. Le revêtement éclate libérant la pièce métallique coulée solidaire de la tige et de ses masselottes, puis elle est brossée, nettoyée, décapée avec une solution appropriée, rincée à l’eau courante et vérifiée sur le modèle avant son traitement thermique éventuel.
B. Maquettes importantes (Châssis coulé, grandes travées de bridges)
Pour avoir une fidélité maximum, la maquette ne doit pas se déformer. Etant donné ses dimensions importantes il est indispensable qu’elle reste sur le modèle et que l’ensemble soit mis en revêtement.
Les modèles en plâtre ne pouvant pas supporter de hautes températures, il est nécessaire de faire un duplicata en revêtement du modèle original.
1. Confection du duplicata
- Cas des alliages précieux : Une empreinte du modèle original sera prise à l’aide d’un hydrocolloïde réversible et cette empreinte sera moulée ensuite avec un revêtement compensateur au plâtre.
- Cas des alliages communs type chrome-cobalt : l’empreinte aux hydrocolloïdes sera moulée avec un revêtement au silicate ou au phosphate.
Lorsque le duplicata en revêtement a durci, la maquette en cire est confectionnée sur ce modèle, puis munie de plusieurs tiges de coulée préfabriquées de longueur convenable et de diamètre important (3 à 4 mm), placées au niveau des parties épaisses.
De plus afin de permettre l’échappement des gaz lors de la coulée, on ajoutera avant la mise en revêtement plusieurs tiges aux endroits adéquats pour servir ultérieurement d’évents.
2. Mise en revêtement
Le duplicata en revêtement muni de sa maquette est coffré par un large cylindre et rempli de revêtement relativement fluide.
Après durcissement du revêtement, évacuation de la cire, séchage du revêtement au four un peu au-dessus de 170 °C, la température du four est portée progressivement à 850 °C.
Le reste des étapes est identique à la coulée des petites pièces.
IV. Défauts de fonderie
Les qualités que nous exigeons de nos pièces coulées peuvent se schématiser comme suit :
- Sur le plan géométrique, la condition fondamentale est la reproduction la plus parfaite possible des formes et des dimensions du modèle buccal.
- Sur le plan mécanique, son homogénéité structurale doit être en rapport avec les efforts qu’elle sera amenée à subir en bouche.
- Sur le plan physicochimique et électrochimique, l’état de surface doit être le plus parfait possible afin d’éviter les phénomènes de corrosion.
- Sur le plan biologique, les exigences précédentes sont accrues par la nécessité de leur tolérance dans la cavité buccale, pour les phénomènes de conductibilité, dilatométrie thermique et la cytotoxicité.
A. Défauts éventuellement liés à la fusion
1. Inclusion gazeuses ou soufflures
Les gaz provenant soit de la source de chaleur, soit de l’air atmosphérique sont solubles dans de nombreux métaux à l’état liquide, cette solubilité est une fonction croissante de la température.
Ce défaut est aggravé si l’alliage contient en solution des éléments susceptibles de se combiner et de donner des composés gazeux. La présence de cire peut être à l’origine d’inclusion de gaz carbonique.
- Sur le plan pratique, les soufflures sont mécaniquement dangereuses, elles peuvent apparaître en surface lors du polissage et entraîner une corrosion, des stases alimentaires et une esthétique déplorable.
Afin d’éviter ces inclusions, il faudra couler à une température aussi basse que possible, opérer la fusion avec un métal dégraissé, protéger le métal en fusion avec un flux réducteur (borax), et utiliser des évents systématiques.
2. Inclusions solides
Les inclusions solides sont des hétérogénéités qui affectent le métal en certains endroits. Il peut s’agir d’oxydes insolubles de l’alliage lui-même, des débris de flux ou de revêtement, ou encore celles entraînées par la dissociation du liant plâtre de certains revêtements aux alentours de 1000 °C.
Afin de les éviter, il convient de placer la tige de coulée de telle sorte que le jet de métal en fusion frappe les parois du moule tangentiellement, éviter les revêtements à liant plâtre lorsque la température de fusion est élevée, et faire en sorte que la quantité de flux désoxydant ne soit pas trop importante.
3. Le manque de coulabilité
La reproduction des détails de la pièce coulée est fonction de la coulabilité de l’alliage utilisé.
La coulabilité est fonction de la tension superficielle, la température (l’alliage est bien fluide entre 50° et 100 °C au-dessus de la température de début de solidification) et de la présence d’oxydes nuisibles tel que l’oxyde de cuivre dans les métaux précieux, et qui les épaissit.
Sur le plan pratique, une mauvaise coulabilité aboutit à des pièces incomplètes.
Afin d’éviter cela, il faut :
- Couler chaque alliage à sa température idéale (en four à induction à haute fréquence)
- Pratiquer la fusion en atmosphère réductrice
- Couler en moule chaud, multiplier les tiges de coulée et les raccourcir pour diminuer le chemin à parcourir.
B. Défauts éventuellement liés à la solidification
1. Le phénomène de retrait
Lors du passage de l’état liquide à l’état solide la force d’attraction mutuelle des atomes, libérée des contraintes thermiques provoque un retrait. Le retrait commence faiblement depuis l’état liquide et se poursuit jusqu’à la fin de la solidification où il atteint son maximum.
Ce retrait est de l’ordre de 2 % à 5 %. Il se produit à trois stades :
- De l’état liquide vers le liquidus (à ce stade, il peut être atténué par un apport de métal fondu supplémentaire via la nourrice)
- Dans l’intervalle liquidus-solidus
- De solidus à température ambiante (fonction du coefficient de dilatation thermique)
La seule possibilité de compensation du retrait reste en ce qui nous concerne, l’utilisation des revêtements compensateurs.
Les retassures
C’est la première conséquence du retrait.
Chaque fois qu’une nouvelle couche se solidifie, le niveau du métal liquide restant baisse d’une hauteur qui correspond à la contraction des couches solides sous-jacentes et au retrait de la couche qui vient de se solidifier.
Les retassures sont évitées par l’adjonction à la tige de coulée d’un large réservoir (nourrice) dont la masse sera suffisante pour qu’elle se solidifie moins vite et nourrisse la retassure.
Les microretassures
Elles correspondent au niveau microscopique aux macroretassures. La cristallisation se fait à partir de germes selon un processus dendritique. Si cet enchevêtrement devient si serré que le liquide ne peut plus couler à travers les cristaux, le métal liquide se solidifie en laissant des vides : ce sont les microretassures.
Afin de les éviter, il faut choisir une tige de coulée de diamètre suffisant en fonction de l’importance de la pièce, et la faire aboutir sur une partie épaisse de la pièce.
Criques et gauchissements
Théoriquement, le refroidissement est plus lent dans les parties épaisses que dans les parties minces de la pièce coulée. Quand les parties épaisses refroidissent à leur tour, elles exerceront sur les parties minces des tensions importantes susceptibles de les déformer et d’y provoquer des criques (fissurations), voire des gauchissements.
Sur le plan pratique, il faudra étudier soigneusement la forme des pièces en évitant les angles vifs et les inégalités brusques de la maquette en cire dans la mesure du possible.
C. Défauts liés à la solidification
1. Non conformité de la composition chimique globale
Peut être due à l’oxydation d’un élément non noble ou la volatilisation d’un constituant de l’alliage.
Comme ces défauts perturbent les propriétés mécaniques, il ne faudra pas utiliser de déchets de coulées anciennes.
2. Ségrégation
C’est l’apparition de différences de concentration d’un certain élément dans une même phase au cours de la solidification.
Elle est dite mineure si elle se produit à l’échelle moléculaire ou majeure quand elle s’observe au niveau de la pièce coulée.
La ségrégation est due au refroidissement, au centre on trouvera des cristaux à forte concentration de composant ayant un point de fusion élevé, à la périphérie des composants ayant un point de fusion bas.
La ségrégation peut entraîner des fissures profondes dans l’alliage et l’endommager.
Le plus souvent elles ne peuvent pas être évitées, mais on y remédie avec des traitements thermiques ultérieurs.
Fonderie de précision à la cire perdue et défauts de fonderie
La prévention carieuse repose sur une éducation efficace du patient et un suivi régulier.
Une anamnèse détaillée permet d’éviter de nombreux pièges diagnostiques en pratique quotidienne.
La gestion du stress pré-opératoire améliore significativement l’expérience du patient.
Les matériaux biocompatibles modernes offrent des alternatives intéressantes aux restaurations traditionnelles.
Une bonne ergonomie de travail protège le praticien des troubles musculo-squelettiques.
L’implantologie requiert une planification rigoureuse et une maîtrise de l’ostéintégration.
L’approche multidisciplinaire devient incontournable pour les cas complexes de réhabilitation orale.
Fonderie de précision à la cire perdue et défauts de fonderie
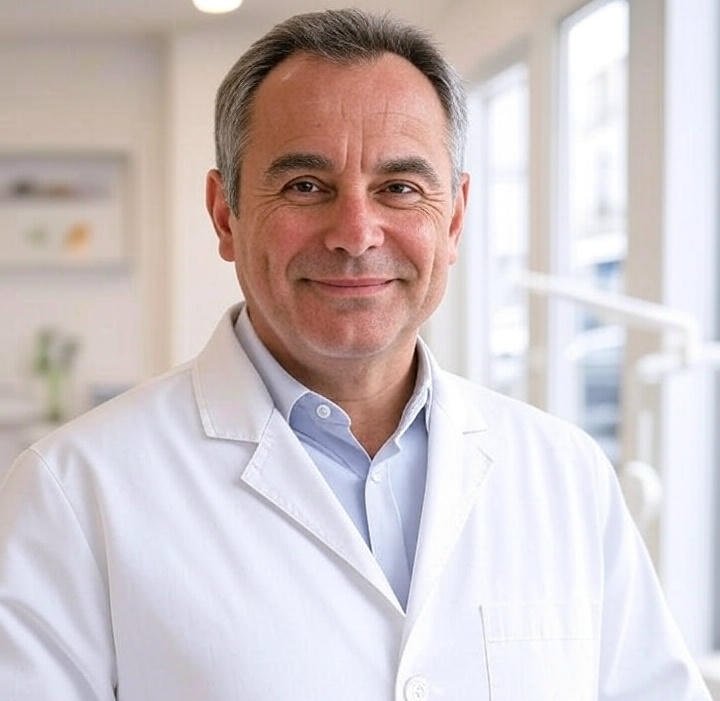
Dr J Dupont, chirurgien-dentiste spécialisé en implantologie, titulaire d’un DU de l’Université de Paris, offre des soins implantaires personnalisés avec expertise et technologies modernes.